The manufacturing of a pure wool quilt is done in several stages that involve several machines and know-how. We open the doors of our workshop to show the realization of these steps by our production team in Belgrade.
1 – Stacking of the fabric in successive layers
The first step is to cut the fabric in successive layers on the cutting bench. Everything is based on a cutting plan based on a production sheet and the width of the fabric. Our manufacturing is artisanal and this operation is done by hand. On larger productions it exists automated cutting benches.
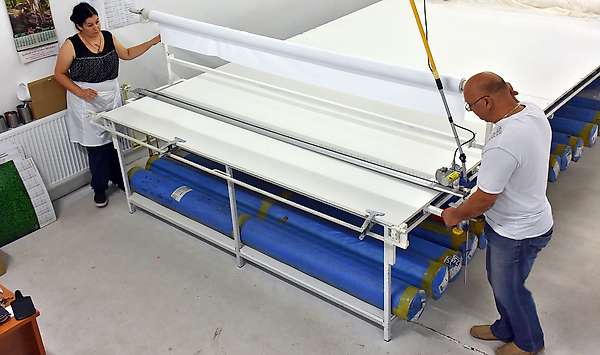
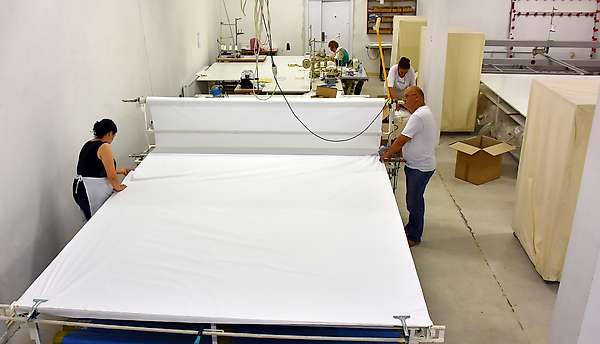
2 – Marking and cutting of the parts
Once the fabric is stacked in the right number of layers, the cutting plan is drawn to delimit the different pieces. If the quilts produced do not occupy the full width of the fabric, the rest of the fabric is used for other products such as pillows or piping.
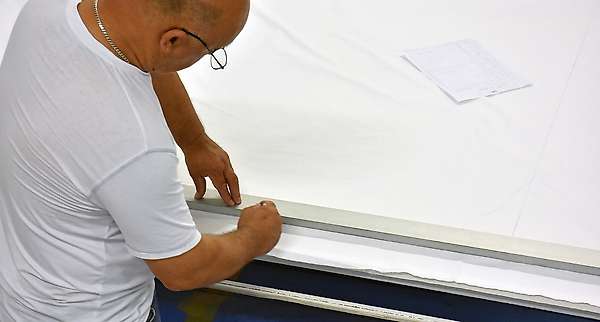
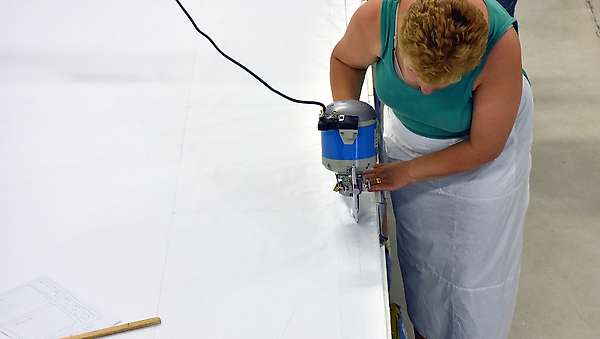
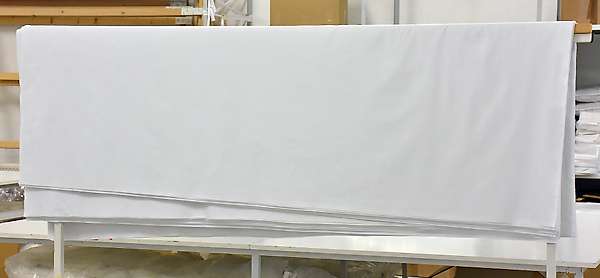
3 – Setting up wool for a duvet
The making of a duvet starts by putting the under layer fabric on the table. Then, the woolen layer is placed on the fabric and cut to the correct size. One wool layer is about 200g/m2. Depending on the type of duvet produced (Ninaja 200g/m2, Hajla 400g/m2 or Maja 600g/m2), 1, 2 or 3 layers of wool are used. In this production, it is Hajla with 2 layers of wool that was produced.
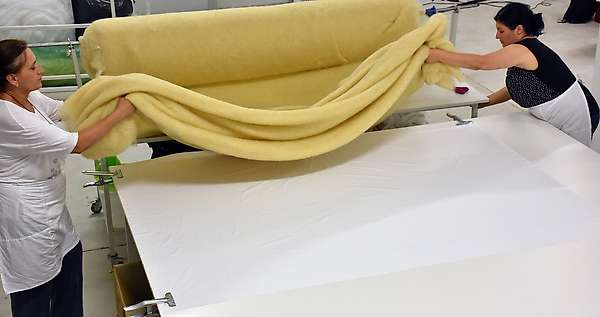
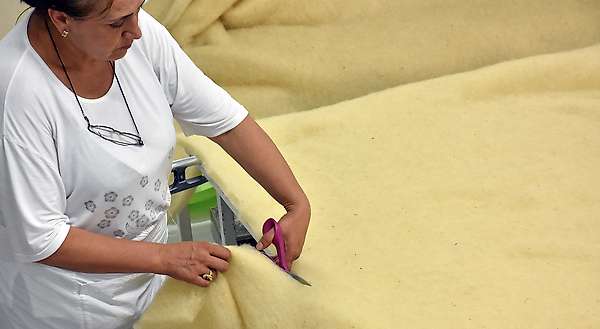
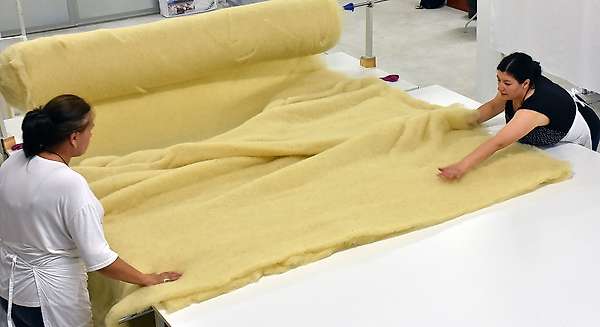
4 – Putting the quilt on the quilting frame
Once the quilt is assembled, small cloth pegs are placed on its periphery to hold the fabric and the wool. It is then placed on a quilting frame. We have fabricated our quilting frames ourselves to be exactly adapted to our manufacturing. They are made of wood, with metal needles on which the quilt is stitched to hold it.
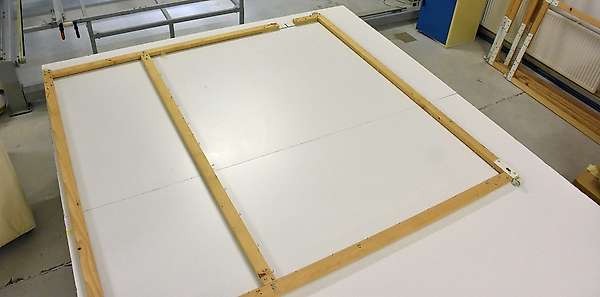
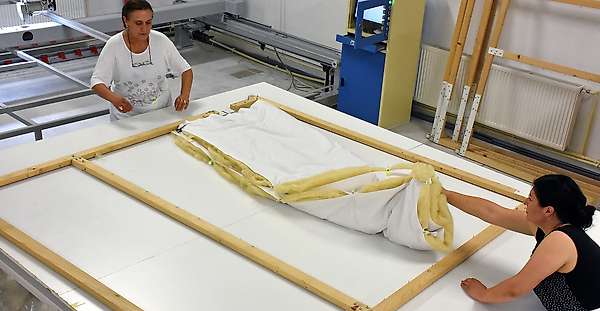
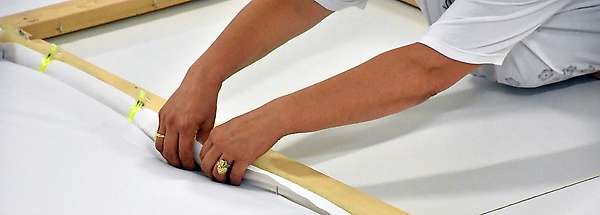
5 – Quilting the duvet
The frame is placed on the machine that performs the quilting. There are basically 2 techniques for quilting: continuous and using a frame. The continuous industrial quilting is not adapted at all to the delicacy of woolen layers. The handmade quilting on frame is the one that gives the best result.
The quilting machine is computer controlled. We have realized our programs ourselves so that they are completely original and perfectly suited to our needs.

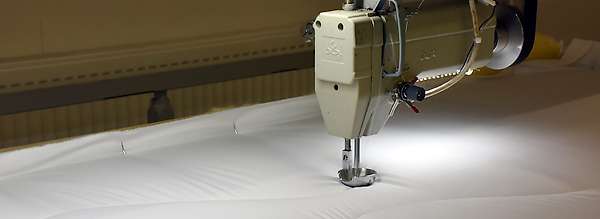
6 – Cutting the duvet to dimensions
Once the quilting is completed, the duvet is taken out of the frame to go to contours cutting. This step ensures the right dimensions, having straight edges and removing the part of the fabric stitched by the needles of the frame.
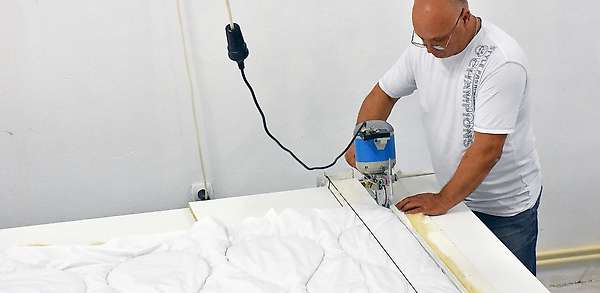
We have built a specific cutting ban that guarantees a fast, safe, straight cut.
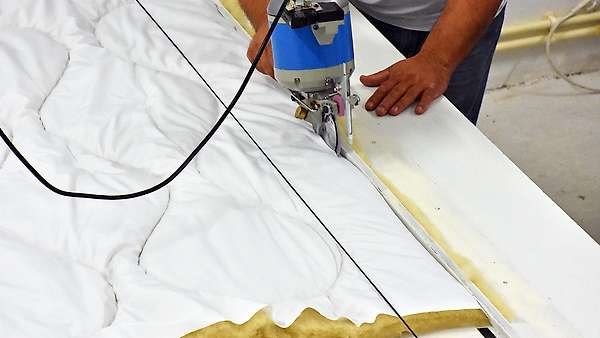
The last part of the cutting for the duvets is the rounding of the corners. This facilitates the sewing of the piping and gives a nice aesthetic to the product.

7 – Laying labels and piping
With the duvet cuts to the right size, the last stage of manufacturing is to sew labels and piping all around. It is an essential step which ensures the wool will stays in place all around the quilt. We use a powerful triple drive machine for this job.
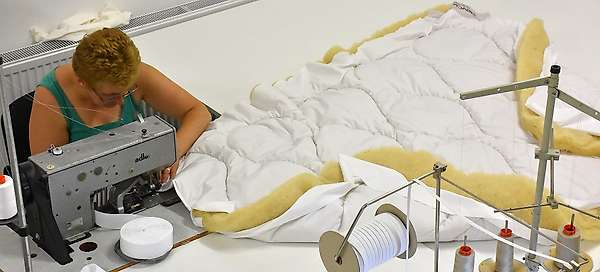
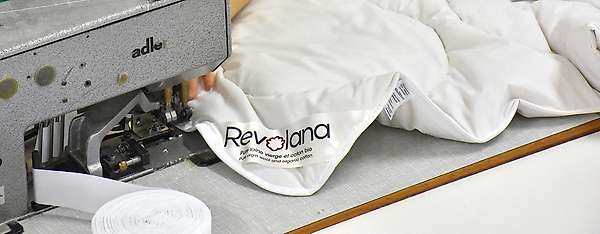
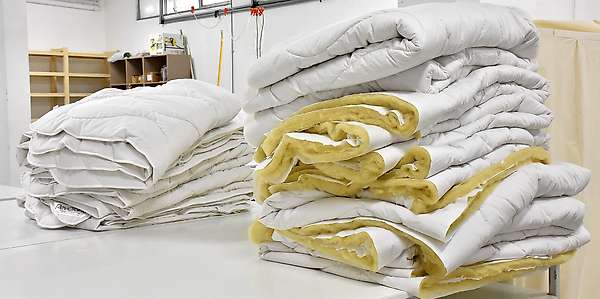
8 – Packaging of the finished product
The duvets are finally folded manually and packaged in a bag adapted to their size.
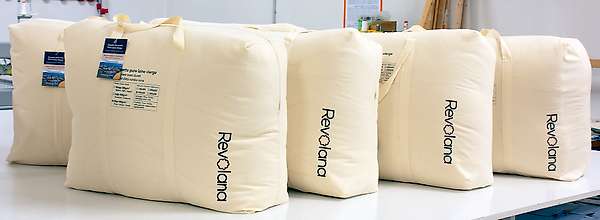